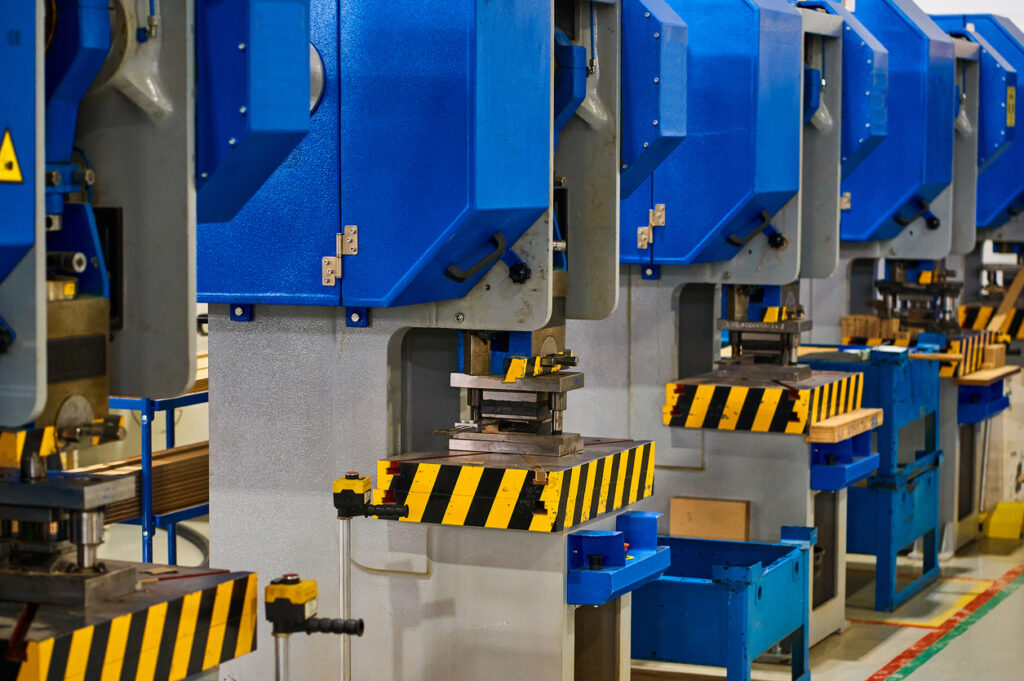
Stamping presses have a significant role in manufacturing, and bring efficiency and precision to the production of metal stamped components and assemblies. This piece of equipment is invaluable in metal stamping manufacturing, and is used to shape metal into the desired dimensions. The press forces metal in between a die and a punch, applying pressure until the workpiece transforms into the required shape.
There are various types of stamping presses: mechanical, hydraulic, and mechanical servo presses are a few examples. Here, we will dive into how these vital pieces of equipment contribute to the quality of precision metal stamped parts and how HTT can optimize the value of your next project.
HTT knows how to produce metal stamped parts that adhere to a higher standard of excellence. Reach out to us today to learn more about how we can help your next project.
Examining Different Stamping Presses and Their Role in Manufacturing
Mechanical presses are efficient, and well-suited for high-volume production. These presses produce reliable and consistent metal stamped parts, and the speed in which they operate make them ideal for industries which require bulk parts, such as the automotive or industrial markets.
Hydraulic presses use hydraulic power to generate force and are a more flexible option, making it an ideal piece of equipment for parts with complex geometries. Mechanical servo presses are also efficient and precise, and utilize high capacity motors. These presses offer precision and can also conserve more energy than other types of presses.
Presses are used within multiple industries, including power generation, water treatment, and lawn and garden. You can find metal stamped components in brackets, hinges, enclosures, brackets, and more.
Exploring How Presses Can Boost Quality and Performance
Modern stamping presses operate at high speeds and some even utilize automation, resulting in more efficient production and shorter lead times because of reduced human error. Consistent quality reduces defects and optimizes the overall quality of each component. These machines are precise, reducing the need for reworks, and in the process, lowering both labor costs and material waste, making this an affordable manufacturing method.
In addition to boosting both precision and efficiency, stamping presses can result in sustainable manufacturing solutions. Presses reduce material scrap, and since these presses are typically durable and long-lasting, you can also expect lower maintenance or replacement costs. The benefits of these machines are vast, and they can craft custom metal stamping solutions that are tailored to your specific needs.
Partner with HTT for Metal Stamping Solutions that Impress
HTT understands how stamping presses can boost precision and efficiency, and we’re prepared to help customers from a wide range of industries with solutions that meet their specifications. We have over 40 metal stamping presses ranging from 25 to 500 tons, and can work with a variety of materials: aluminum, stainless steel, brass, coated materials, and more. We also offer deep drawn stamping services and our team of engineers have developed deep draw dies with a draw depth of up to 6”.
Preparation is key for success, and we offer comprehensive design consultations to ensure that success before your project even moves into production. We take your product from concept to completion, and our start-to-finish support includes powder coating, metal fabrication, wire EDM, and more. With our end-to-end services, you can save time, money, and headaches, all while enhancing the quality of your metal stamped components and assemblies.
With our advanced equipment and expert capabilities, we can enhance the precision and efficiency of your next project. Get in touch with us today to learn more.